A conformable dielectric tape solution
EV battery pack voltages are increasing, resulting in greater pack energy density and improved vehicle performance. With this increase, however, comes a greater need for dielectric solutions that are not only reliable and durable, but complement modern pack design and the needs of manufacturing processes.
The Avery Dennison Volt Tough Portfolio of dielectric PSA tapes for EV batteries addresses these needs. The next-generation Volt Tough
Stretch offering provides manufacturers with a dielectric solution that’s stampable, conformable, resistant to tearing, and accommodates the heat flow needs within the pack.
Prevention of electrical arcing in EV battery packs is critical
The evolution of EV battery pack voltage and energy density has been pivotal in enhancing vehicle performance and range.
Today’s EVs utilize battery packs operating at 400V or 800+V. This enables faster charging times and more efficient power delivery to the motor. Concurrently, improvements in energy density — the amount of energy stored per unit of mass or volume — have allowed for lighter, more compact battery packs that can store more energy.
Prevention of electrical arcing has always been a core safety concern in battery pack design. With this growth in pack performance, however, prevention has become imperative to prevent short circuits; thermal runaway; or electrical hazards for the driver, passengers, and service technicians.
An overview of traditional dielectric protection solutions
Robust, cost-effective dielectric protection solutions are thus needed, and EV battery manufacturers have employed a variety of methods. The most common are dielectric coatings (applied by spraying or dipping), or pressure-sensitive (PSA) tapes utilizing dielectric films such as PET or polyimide.
These coatings and tapes can be applied to the internal components of a battery pack to prevent unintended electrical conduction. They ensure battery packs can operate effectively in diverse conditions, improving their performance and longevity, and enhancing driver and passenger safety.
Dielectric coatings have enjoyed an added advantage over film tapes due to their ability to be easily applied to stamped metal parts with complex geometries. As manufacturers continue to evolve their designs, conformability has become an increasingly important requirement for dielectric materials.
Shortcomings of traditional conformable dielectric solutions
Dielectric coatings can indeed be effective electrical insulators in modern EV batteries, and they are highly appealing due to their conformability. However, these coatings do have shortcomings that can affect the manufacturing process and the overall effectiveness of the battery pack design.
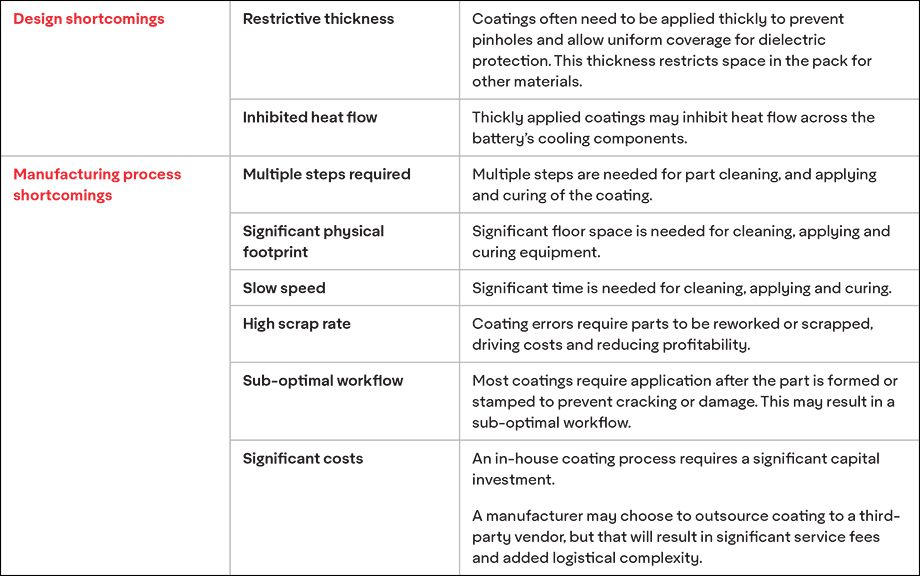
Better conformable dielectric solutions are needed that allow manufacturers to avoid these shortcomings. PSA tapes with stampable dielectric films, designed to be stamped and formed with their underlying substrates, are just such a solution.
Evaluating stampable dielectric tapes against competing dielectric technologies
A new type of PSA tape technology is now available that addresses these shortcomings. This tape features a highly conformable dielectric film facestock that is fully compatible with metal stamping processes.
The tape can be applied to a metal blank (manual or automated application process), then stamped along with the blank. The result is a formed metal part with dielectric protection already applied. Unlike coatings, the PSA tape and its conformable dielectric film resist damage or cracking in the press.
In testing completed at the Avery Dennison Performance Tapes laboratory, an ISO-9000 facility, samples of a PSA-based dielectric protection solution were applied to aluminum sheet metal blanks. The samples were then stamped to test the durability of the tape under various pressures typical of industrial metal stamping. In all cases, the PSA solution withstood applied pressures, even in extreme instances when sufficient pressure was applied to crack the aluminum substrate.
Here’s how this new technology compares to traditional dielectric solutions.
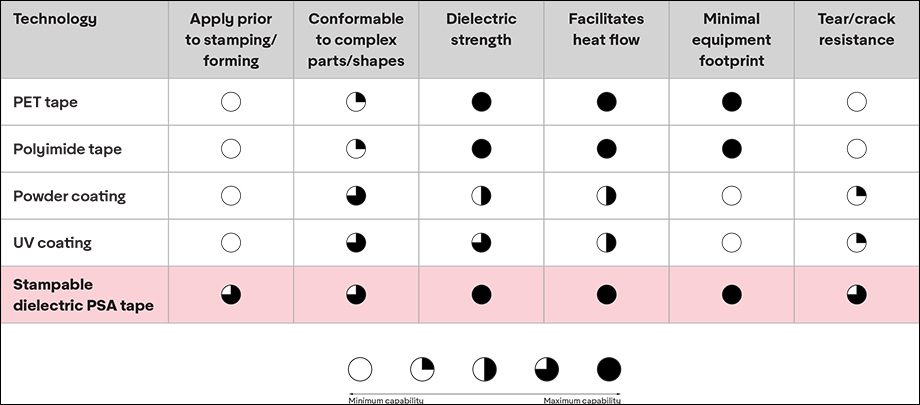
There are a host of challenges associated with dielectric coatings, including:
- Limited assembly line flexibility
- Increased waste and cost
- Lack of conformability to complex parts/shapes
- Limited space in battery pack due to dielectric coating thickness
- Large physical equipment footprint
- Easily torn or cracked
Thankfully, Stampable dielectric PSA tapes provide an alternative to the above challenges, through the following solutions:
- Less labor-intensive process and faster assembly line
- Lower scrap rates and higher production rates
- Stampable tapes combine high elongation at break and high tear resistance
- Stampable dielectric PSA tape provides significantly more dielectric strength per unit of thickness compared to a typical dielectric coating
- Physical footprint for tape application is significantly less than what is required for coating application
- Very high elongation at break combined with high tear resistance.
Introducing Next-Generation Volt Tough Stretch | A PSA-based stampable dielectric solution from Avery Dennison
Avery Dennison has developed and introduced a PSA-based dielectric protection solution. Part of the company’s Volt Tough portfolio, this tape is the next generation of the Volt Tough
Stretch PSA dielectric tape (Avery Dennison part number FT 0031).
This solution is designed to accommodate a wide range of needs while addressing key challenges for electrical insulation in battery packs. Importantly, this new tape solution is highly compatible with metal stamping processes and other metal-forming techniques.
Put simply, next-generation Volt Tough Stretch can be applied to a metal blank, then stamped into a complex shape without significant risk of the tape cracking, tearing, or sustaining any other type of damage.
Like all PSA tapes, next-generation Volt Tough Stretch is easy to apply and reposition, features a thin profile, and is durable for the life of the battery.
Applications
Next-generation Volt Tough Stretch can be used for bonding and protection in various applications throughout a battery pack. It has been increasingly used with cooling plates and pack structures.
- Pack structural components
- Flexible and rigid busbar and cell connection systems in EV battery assemblies
- Various cooling components, including chill plates and cooling ribbons
Avery Dennison solutions for EV battery manufacturing
The Avery Dennison EV Battery portfolio includes various functional bonding and protection tapes built on multiple PSA technologies. These are engineered to make EV batteries safer, more efficient and easier to assemble.
The portfolio can help manufacturers solve some of the most common challenges in battery design and construction, including reducing flammability, boosting dielectric strength and design/assembly optimization.
Beyond bonding
Avery Dennison Performance Tapes offers extensive support beyond its product portfolio. This includes providing converters and end users with access to testing and collaboration with subject matter experts to develop unique solutions for EV Battery applications.
Contact Avery Dennison to learn more
If you’re an OEM, automotive tier supplier or converter representative looking to better understand the potential for PSA tapes in EV batteries, please contact us directly at dustin.winter@averydennison.com or max.vanraaphorst@averydennison.com.
To learn more about Avery Dennison Performance Tapes’ solutions, visit www.tapes.averydennison.com/evbattery.