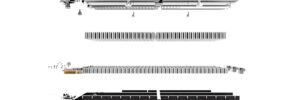
Battery inspection technology firm EVident Battery has closed a $3.2-million seed funding round to accelerate the development of its products.
The round was led by Ibex Investors, and included Nationwide Ventures, Automotive Ventures, Avesta Fund and angels in the EV space.
EVident Battery has developed non-destructive EV battery pack inspection systems that execute in less than two minutes. Non-cell failures have previously been undetectable without destructive teardown, according to the company.
EVident Battery has launched a pilot product, marking a step toward commercialization, enabling the company to validate performance, refine its AI models and scale deployment.
Jeff Peters, Partner and Head of Mobility VC at Ibex Investors, is joining EVident’s Board of Directors. “Most attention from automakers and startups is focused on cell-related battery state of health. However, an EV is much more than a collection of cells,” said he. “EVident has created a unique diagnostic for the structural integrity of the entire battery pack. We are excited about the opportunity this technology unlocks in manufacturing quality control, ongoing monitoring, the second-hand EV market, and ultimately end-of-life disposition.”
“This funding allows us to accelerate our roadmap, bringing to market battery inspection technology that is not only high-performing but also environmentally conscious,” said Jinqiang Ning, CEO of EVident Battery. “Our goals are to standardize EV battery service and inspection and to build a centralized EV battery database for full transparency.”
Source: EVident Battery